MIG Welding vs Arc Welding | Save Money, Cost-Effective Welding Guide
Welding is a critical process in many industries, from manufacturing and construction to automotive and aerospace. When choosing between various welding techniques, cost-efficiency is often a major consideration. Among the most popular welding methods are MIG (Metal Inert Gas) welding and arc welding (commonly referred to as stick welding). While both have their benefits (MIG Welding vs Arc Welding), MIG welding can offer several financial advantages over traditional arc welding. These savings stem from factors like speed, material efficiency, labor costs, and equipment longevity. Let’s take a deeper look at how MIG welding can help businesses save money.
1. Faster Welding Speed and Increased Productivity
One of the key advantages of MIG welding is its faster welding speed compared to arc welding. MIG welding uses a continuously fed wire electrode, which means the welder doesn’t need to stop and replace electrodes frequently as with arc welding. This results in continuous and uninterrupted welding.
- Higher deposition rate: MIG Welding vs Arc Welding, MIG welding typically has a higher deposition rate, meaning that more material is deposited in less time. The process is more efficient, especially on thicker materials, allowing welders to complete tasks faster.
- Fewer stops for electrode changes: In arc welding, the welder has to stop and replace the stick electrode after it is used up, which adds downtime. In contrast, MIG welding’s continuous wire feed reduces these interruptions.
- Reduced downtime: Faster welding speeds mean more time can be spent on the actual welding process, and less time is needed for setup or idle periods between welds. This translates into increased productivity and lower labor costs for employers.
2. Reduced Material Waste and Cost-Effective Consumables
Material waste is a significant factor when calculating the overall cost of welding, and MIG welding often proves to be more material-efficient than arc welding for several reasons:
- End Stub Wastage: The end stub of an arc welding electrode is around 5% to 10% of the electrode. This part is always thrown away and a new electrode is taken. This can be completely avoided in MIG Welding as it’s a continuously wire fed process and there are no stubs to waste. A straight forward material savings.
- Less spatter: MIG welding produces significantly less spatter than arc welding. The reduced spatter means less cleanup and less material loss. In arc welding, the amount of spatter can increase, especially if the technique or settings are not optimal. This leads to wasted filler material that doesn’t contribute to the weld.
- Cleaner welds: MIG welding creates cleaner welds with a more controlled heat input, reducing the need for post-weld cleanup. In arc welding, the presence of slag and excess spatter often requires extensive grinding, which uses additional labor, equipment, and consumables.
- Flux coating of electrode: When we buy electrodes, the cost is for metal and the flux coating on the electrode. One welded the metal gets deposited and the flux vaporises and certain part forms slag which is then removed. On the other hand when we buy MIG or MAG consumables solid wire is purchased and the entire weight of consumable purchase is utilised on the JOB. Thus it’s a more cost effective purchase of consumables.
- Shielding gas usage: While MIG welding requires a shielding gas (argon or a mix of gases), it is used more efficiently than the flux used in stick welding. The cost of the shielding gas can be offset by the increased productivity and less waste.
3. Reduced Labor Costs Due to Ease of Use | MIG Welding vs Arc Welding
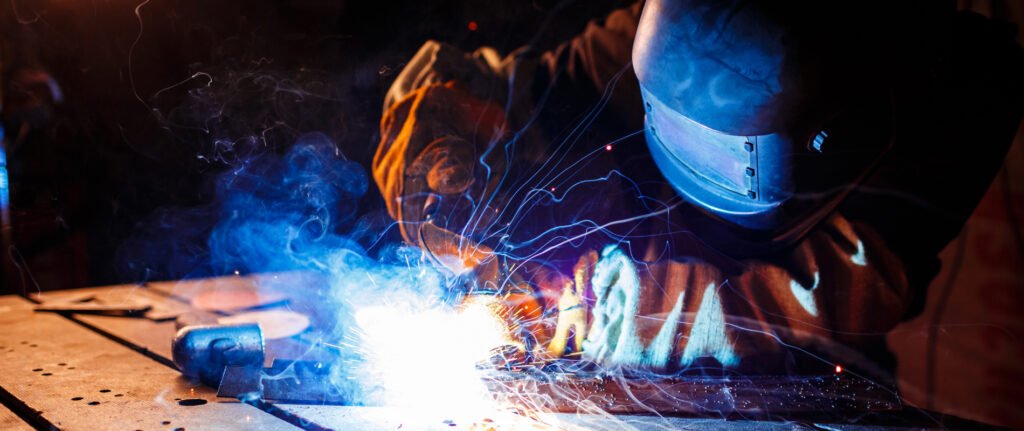
MIG welding tends to be easier to learn and operate compared to arc welding, which can translate into lower labor costs. Here are some reasons why:
- Shorter learning curve: MIG welding is considered easier to master than arc welding because it has a more stable arc and doesn’t require the welder to constantly adjust the angle, speed, or electrode position as much. New workers can be trained more quickly, leading to a lower training cost and faster integration into the workforce.
- Less skill-dependent: While arc welding requires more skill to maintain a stable arc and prevent defects, MIG welding is more forgiving, which can reduce the chances of mistakes. This means fewer rework costs and higher-quality welds from less experienced workers.
- Fewer weld defects: MIG welding produces smoother, more consistent welds with fewer defects. This reduces the amount of rework needed, which, in turn, saves time and money. Arc welding, on the other hand, can result in more weld defects, requiring additional time for correction, inspection, and testing.
4. Versatility and Application Range
MIG welding is versatile and can be used on a wide variety of metals, including mild steel, stainless steel, aluminium, and even copper alloys. MIG Welding vs Arc Welding, Its adaptability helps businesses save money because they don’t need to invest in multiple welding processes or equipment for different materials.
- Fewer machines required: MIG welding machines can handle a wide range of materials and thicknesses. In contrast, arc welding is often better suited for heavier materials, and multiple processes or equipment may be required to weld thinner metals or more specialized alloys.
- One setup for multiple jobs: MIG welding offers the flexibility to switch between different material types and thicknesses without requiring major adjustments or new equipment, unlike arc welding, which may require more specific setups or even different welding rods for different jobs. This versatility reduces the need for additional equipment purchases and maintenance.
- CCCV Combi machines: APS Welding machine are all combi machine with capability to perform both MIG / MAG as well as ARC Welding operations from a single power source. This makes them one of the most versatile products. Always choose CCCV instead of CV machines for better versatility and multifunctional capabilities.
6. Energy Efficiency
MIG welding is generally more energy-efficient compared to arc welding due to its higher arc stability and faster operation. Because MIG welding requires less time to complete a weld, the total energy consumption for a particular job can be lower than for stick welding, especially for larger production runs.
- Lower electricity usage: MIG welders typically consume less electricity overall than arc welders. This is due to the efficient nature of the process, as MIG welding uses a constant voltage power source, which is more stable and effective than the fluctuating current in arc welding.
- Faster processes mean lower energy costs: As mentioned, the quicker welding speed of MIG welding reduces the overall time spent on each weld, resulting in lower energy consumption.
7. Reduced Post-Weld Treatment Costs
The amount of post-weld treatment or cleanup required after the welding process can also significantly impact overall costs. As previously mentioned, MIG welding creates cleaner welds with minimal spatter, meaning:
- Less need for grinding or polishing: Post-weld cleanup is typically much easier and faster with MIG welding compared to arc welding, where extensive grinding and polishing may be required to remove slag and smooth out the weld. This reduces the need for additional labor and equipment like grinders and sanding materials.
- Reduced rework: The clean, precise nature of MIG welding also reduces the need for rework caused by poor weld quality, further saving on labor and materials.
Conclusion: Why MIG Welding Is More Cost-Effective
MIG Welding vs Arc Welding, While the upfront cost of MIG welding equipment might be higher than that of arc welding, the overall savings in terms of time, material efficiency, labor costs, and equipment maintenance make MIG welding a more cost-effective option in many cases. Its higher welding speed, cleaner welds, reduced spatter, and lower need for post-weld treatment all contribute to lower operating costs. Additionally, MIG welding’s versatility across a wide range of materials and thicknesses further enhances its cost-efficiency.
Ultimately, for businesses looking to streamline their welding processes and reduce long-term expenses, MIG welding presents a compelling option, especially when high-quality, efficient, and consistent welds are required.